How to select stepper motor for CNC?
How to select stepper motor for CNC?
CNC (Computer Numerical Control) machines rely on stepper motors to drive the movement of the machine's axes. The selection of the right stepper motor for a CNC
machine is crucial to ensure smooth and accurate operation. There are several factors to consider when selecting a stepper motor for a CNC machine, including torque,
step angle, holding torque, speed, size, and driver compatibility. In this article, we will discuss each of these factors in detail to help users choose the right
stepper motor for their CNC machine.
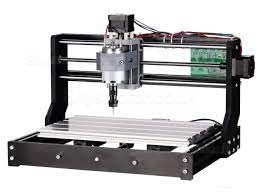
Torque
Torque is the most important factor to consider when selecting a stepper motor for a CNC machine. Torque is the rotational force that drives the motor shaft and
determines the amount of weight the motor can handle. The amount of torque required will depend on the weight of the machine's moving parts and the cutting force
required for the materials being used. It is crucial to choose a stepper motor with sufficient torque to ensure that the CNC machine operates smoothly and accurately.
The torque output of a stepper motor is typically listed in oz-in (ounces per inch) or Nm (Newton-meters). The required torque will vary depending on the CNC machine's
application. For example, a CNC router that cuts through thick wood or metal will require a higher torque motor compared to a 3D printer that prints small plastic
parts. It is important to ensure that the selected stepper motor provides sufficient torque to handle the machine's workload.
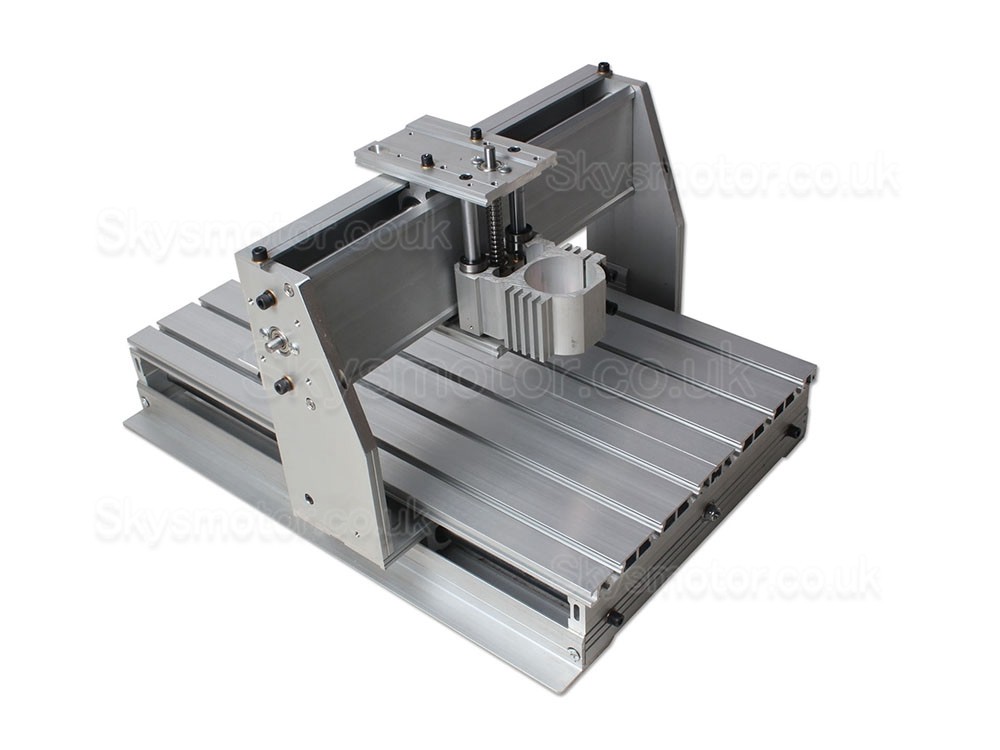
Step Angle
The step angle of a stepper motor refers to the angle between each step of the motor shaft. Most stepper motors have a step angle of 1.8 degrees, which means that it
takes 200 steps to complete a full revolution. However, stepper motors with a step angle of 0.9 degrees or even 0.45 degrees are also available. A smaller step angle
allows for finer control and greater accuracy, but it also requires more steps to complete a full revolution. It is important to balance the step angle with the
required speed and torque of the CNC machine.
The number of steps per revolution determines the machine's resolution, or the smallest distance the machine can move. For example, a stepper motor with a step angle
of 1.8 degrees will move the machine 0.9 degrees with each step, which translates to 0.0078125 inches of movement per step. A smaller step angle will increase the
machine's resolution, but it may also decrease the motor's torque output.
Holding Torque
Holding torque refers to the amount of torque that the stepper motor can generate when it is stopped. This is important for the CNC machine to maintain its position
when not in motion. It is crucial to choose a stepper motor with a high holding torque to ensure that the CNC machine maintains its position accurately.
The holding torque of a stepper motor is typically listed in oz-in or Nm. The required holding torque will depend on the weight of the machine's moving parts and the
cutting force required for the materials being used.
Speed
The speed of the stepper motor is another important factor to consider when selecting a stepper motor for a CNC machine. The speed of the motor is determined by the
number of steps the motor can take per second. It is important to choose a stepper motor that can provide the required speed for the CNC machine without sacrificing
torque or accuracy.
The speed of a stepper motor is typically listed in RPM (rotations per minute). The required speed will depend on the CNC machine's application. For example, a CNC
milling machine that cuts through thick metal will require a slower speed motor compared to a CNC laser cutter that cuts through thin materials. It is crucial to
choose a stepper motor that provides the required speed without sacrificing torque or accuracy.
Size
The size of the stepper motor is also an important factor to consider when selecting a stepper motor for a CNC machine. The size of the motor will depend on the size
of the machine and the required torque and speed. It is important to choose a motor that is compact enough to fit within the machine without sacrificing performance.
The size of a stepper motor is typically listed in NEMA (National Electrical Manufacturers Association) sizes, such as NEMA 17, NEMA 23, and NEMA 34. The NEMA size
refers to the motor's frame size and mounting dimensions. NEMA 17 is the most common size for CNC machines, due to its compact size and high torque output. NEMA 23 and
NEMA 34 are larger and more powerful, but are typically only used in larger, industrial-grade CNC machines.
Driver Compatibility
The driver is the component that controls the stepper motor. It is crucial to choose a driver that is compatible with the stepper motor and provides the necessary
voltage and current to drive the motor. The driver should also be capable of providing microstepping, which allows for finer control and greater accuracy.
There are several types of driver and controller systems available, including standalone controllers, integrated controllers, and open-source systems like RepRap and
Marlin. The choice of driver and controller will depend onthe CNC machine's application and the user's level of expertise. It is important to ensure that the chosen
driver and controller are compatible with the selected stepper motor and provide the necessary features for the CNC machine's operation.
_______________________________________________________________
skysmotor.co.uk is a professional online supplier of Nema 17 Stepper Motor and Nema 23 Stepper Motor. We offer competitive prices and efficient services to our
customers.